Seamless stainless steel tubes represent one of the most significant innovations in material engineering, playing a crucial role across numerous industries. These precision-engineered components, manufactured without any welding seams, offer superior strength, corrosion resistance, and reliability compared to their welded counterparts.
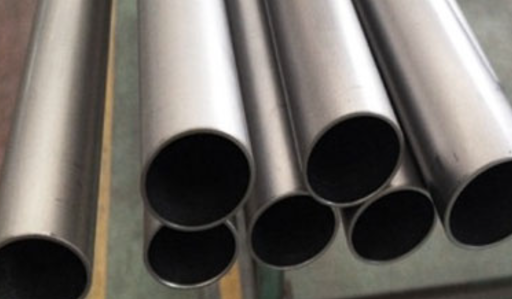
Manufacturing Process:
The production of seamless stainless steel tubes involves a sophisticated process:
- Hot Working
- Solid steel billets are heated to extreme temperatures
- The heated material is pierced using a mandrel
- Initial tube shell is formed through rotary piercing
- Cold Working
- The rough tube undergoes cold drawing
- Multiple passes achieve precise dimensions
- Surface finishing and treatment
Key Properties:
- Mechanical Strength
- High tensile strength
- Superior burst pressure resistance
- Excellent fatigue resistance
- Uniform structural integrity
- Corrosion Resistance
- Outstanding resistance to chemical attack
- Superior performance in marine environments
- Ability to withstand extreme temperatures
- Extended service life in aggressive media
- Quality Characteristics
- Consistent wall thickness
- Smooth surface finish
- Precise dimensional accuracy
- Superior concentricity
Industrial Applications:
- Oil and Gas Industry
- High-pressure pipelines
- Offshore platforms
- Drilling equipment
- Heat exchangers
- Chemical Processing
- Chemical transport systems
- Reaction vessels
- Processing equipment
- Storage systems
- Power Generation
- Boiler tubes
- Heat exchanger tubes
- Nuclear power components
- Steam generation systems
- Aerospace
- Hydraulic systems
- Fuel lines
- Structural components
- Landing gear assemblies
- Automotive Industry
- Fuel injection systems
- Exhaust components
- Structural elements
- Brake lines
Grade Classifications:
Common stainless steel grades used include:
- 304/304L: General purpose
- 316/316L: Enhanced corrosion resistance
- 321: High-temperature applications
- 2205: Duplex for extreme conditions
Quality Standards and Testing:
- Non-destructive Testing
- Ultrasonic examination
- Eddy current testing
- Hydrostatic pressure testing
- X-ray inspection
- Certification Standards
- ASTM specifications
- ASME standards
- API requirements
- ISO certifications
Market Considerations:
- Price Factors
- Raw material costs
- Manufacturing complexity
- Grade selection
- Dimensional requirements
- Market demand
- Supply Chain
- Global availability
- Lead times
- Stock programs
- Custom manufacturing options
- Selection Criteria
- Operating pressure
- Temperature requirements
- Chemical exposure
- Mechanical stress
- Cost considerations
Maintenance and Installation:
- Handling Requirements
- Proper storage conditions
- Protection during transport
- Clean installation environment
- Appropriate tools and equipment
- Installation Best Practices
- Proper alignment
- Correct fitting selection
- Appropriate joining methods
- Quality control procedures
Future Trends:
- Technological Advancements
- Advanced manufacturing processes
- Improved material properties
- Enhanced testing methods
- Automated production systems
- Market Developments
- Growing demand in emerging markets
- Increased focus on sustainability
- Development of new applications
- Enhanced product specifications
Environmental Considerations:
- Recyclability of materials
- Energy-efficient production
- Reduced waste generation
- Sustainable manufacturing practices
Safety Considerations:
- Pressure ratings
- Temperature limitations
- Chemical compatibility
- Installation requirements
- Regular inspection protocols
Conclusion:
Seamless stainless steel tubes continue to be essential components in modern industrial applications. Their unique combination of strength, durability, and corrosion resistance makes them invaluable across numerous sectors. As technology advances and industrial requirements evolve, these products will remain crucial to engineering solutions worldwide.