Stainless steel welding wire plays a crucial role in the fabrication and repair of stainless steel structures and components. As a specialized consumable, it enables joints that maintain the corrosion resistance and mechanical properties that make stainless steel so valuable across industries.
## Composition and Types
Stainless steel welding wires are manufactured to match specific grades of stainless steel. Common varieties include:
– ER308/308L: For welding 304/304L austenitic stainless steel
– ER316/316L: Contains molybdenum for enhanced corrosion resistance
– ER309/309L: Used for dissimilar metal welding between stainless and carbon steels
– ER2209: Duplex stainless steel welding wire for high-strength applications
The “L” designation indicates low carbon content (typically below 0.03%), which helps prevent carbide precipitation and intergranular corrosion in welded joints.
## Applications
These specialized welding wires find applications across numerous industries:
– Chemical processing equipment
– Food and beverage manufacturing
– Pharmaceutical production facilities
– Oil and gas infrastructure
– Nuclear power generation
– Marine environments
– Architectural fabrication
## Selection Factors
Choosing the appropriate stainless steel welding wire requires consideration of:
1. Base metal composition
2. Service environment (temperature, chemicals, etc.)
3. Mechanical property requirements
4. Welding process (TIG, MIG, SAW)
5. Regulatory compliance needs
## Quality Considerations
High-quality stainless steel welding wire should exhibit:
– Consistent chemical composition
– Smooth feeding characteristics
– Clean surface finish free from contaminants
– Proper packaging to prevent moisture absorption
– Traceability through lot numbering and certification
Industry leaders continue to innovate in this field, developing specialized formulations for challenging environments and advancing manufacturing techniques that enhance weld quality and performance.
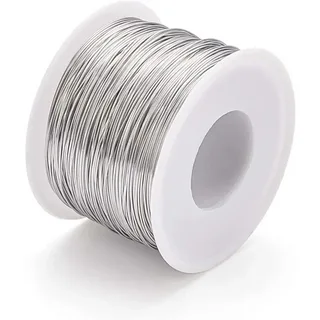