Galvanized square steel is a material that, while often overlooked in everyday life, plays an indispensable role in shaping the modern world. From towering skyscrapers to humble backyard sheds, this versatile and durable material has become a staple in construction, manufacturing, and even artistic design. Its unique properties, derived from a meticulous production process, make it a symbol of human ingenuity in the quest for strength, longevity, and practicality. In this article, we will explore the origins, production, applications, advantages, and future potential of galvanized square steel, shedding light on why it remains a cornerstone of industrial progress.
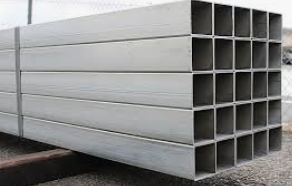
What is Galvanized Square Steel?
At its core, galvanized square steel is a type of steel tubing or structural component with a square cross-section that has undergone a galvanization process. Galvanization involves coating the steel with a protective layer of zinc to prevent corrosion and extend its lifespan. The square shape distinguishes it from other steel forms, such as round pipes or flat sheets, offering unique structural benefits that we’ll delve into later. The zinc coating not only enhances durability but also gives the steel a distinctive, slightly shiny appearance, often recognizable in outdoor structures or industrial settings.
The process of galvanization dates back to the 18th century, credited to Italian scientist Luigi Galvani, whose name inspired the term. However, it was refined over time, particularly in the 19th century, when hot-dip galvanizing—submerging steel in molten zinc—became a standard industrial practice. Today, galvanized square steel is produced in various sizes and thicknesses, tailored to meet the demands of diverse applications.
The Production Process: Strength Through Science
The journey of galvanized square steel begins with raw steel, typically low-carbon steel, which is chosen for its malleability and strength. This steel is first rolled and shaped into a square tube through a series of mechanical processes, including cutting, bending, and welding. The square shape is achieved either by forming flat steel sheets into a tube and welding the seam or by extruding the steel directly into the desired shape.
Once the square steel is formed, it undergoes galvanization. In the hot-dip method, the steel is cleaned to remove impurities like rust or oil, then submerged in a bath of molten zinc at temperatures around 450°C (842°F). The zinc bonds metallurgically with the steel, creating a robust, multi-layered coating. This coating consists of an outer layer of pure zinc and inner layers of zinc-iron alloys, which provide exceptional resistance to rust and wear. Alternatively, some manufacturers use electro-galvanizing, where zinc is applied via an electric current, though this method typically results in a thinner coating.
After galvanization, the steel is cooled, inspected, and cut to size. The result is a product that combines the inherent strength of steel with the protective qualities of zinc—a material ready to withstand harsh environments and heavy loads.

Applications: From Infrastructure to Innovation
Galvanized square steel’s versatility makes it a favorite across industries. In construction, it is widely used for structural frameworks, such as beams, columns, and trusses. Its square shape provides superior torsional stability compared to round tubing, making it ideal for load-bearing applications where twisting forces are a concern. You’ll find it in the skeletons of buildings, bridges, and warehouses, quietly supporting the weight of modern life.
Beyond construction, galvanized square steel shines in outdoor settings. Its corrosion resistance makes it perfect for fencing, gates, and railings, where exposure to rain, snow, and humidity would quickly degrade unprotected metals. Farmers rely on it for livestock enclosures, while homeowners use it for garden trellises or pergolas. In the automotive and transportation sectors, it’s employed in trailer frames, truck beds, and chassis components, valued for its strength-to-weight ratio.
Interestingly, galvanized square steel has also found a niche in creative fields. Artists and designers appreciate its industrial aesthetic and durability, incorporating it into sculptures, furniture, and modern architectural elements. A coffee table with a galvanized steel frame, for instance, blends minimalist design with rugged functionality—a testament to the material’s adaptability.
Advantages: Why Galvanized Square Steel Stands Out
The appeal of galvanized square steel lies in its combination of practical benefits. First and foremost is its corrosion resistance. The zinc coating acts as a sacrificial anode, meaning it corrodes in place of the steel if the surface is scratched or exposed. This self-protecting mechanism ensures longevity, often allowing structures to last decades with minimal maintenance.
Second, its strength is remarkable. Steel itself is renowned for its tensile strength, and the square geometry enhances its ability to resist bending and twisting. This makes it a reliable choice for projects requiring structural integrity under stress. Compared to materials like aluminum or wood, galvanized square steel offers a superior balance of durability and cost-effectiveness.
Third, it’s low-maintenance. Unlike painted steel, which requires periodic recoating, or wood, which demands sealing and pest protection, galvanized steel can endure years of exposure with little upkeep. This makes it an economical option over the long term, especially in harsh climates.
Finally, galvanized square steel is environmentally friendly. Steel is one of the most recycled materials in the world, and the galvanization process adds minimal environmental burden. The longevity of galvanized products also reduces the need for frequent replacements, conserving resources over time.
Challenges and Limitations
Despite its many strengths, galvanized square steel isn’t without drawbacks. The galvanization process, while effective, can be energy-intensive, particularly in hot-dip methods, raising concerns about its carbon footprint. Additionally, the zinc coating can degrade over decades in extremely corrosive environments, such as coastal areas with high salt exposure, eventually exposing the steel beneath.
Welding galvanized steel also poses challenges. The zinc coating can release toxic fumes when heated, requiring proper ventilation and safety precautions. For some applications, alternative materials like stainless steel or composites might be preferred, especially where weight or aesthetics take precedence over cost.
The Future of Galvanized Square Steel
As technology advances, so does the potential of galvanized square steel. Innovations in galvanizing techniques, such as more energy-efficient processes or hybrid coatings (e.g., zinc-aluminum alloys), promise to enhance its performance and sustainability. Researchers are also exploring ways to make the material lighter without sacrificing strength, which could expand its use in aerospace or electric vehicles.
In a world increasingly focused on sustainability, galvanized square steel’s recyclability and durability position it as a material of the future. Urbanization and infrastructure development, particularly in emerging economies, will likely drive demand for this reliable workhorse. Meanwhile, its aesthetic appeal ensures it will continue to inspire designers and architects seeking to blend form and function.
Conclusion
Galvanized square steel may not grab headlines, but its impact is undeniable. It is a quiet hero of the industrial age, supporting the structures we live in, the vehicles we drive, and the spaces we enjoy. Through a marriage of steel’s strength and zinc’s protection, it exemplifies how simple innovations can yield profound results. As we look to the future, galvanized square steel will undoubtedly remain a vital ingredient in the recipe of human progress—unassuming, yet essential, in its square, sturdy glory.