ier, preventing further oxidation and corrosion of the underlying metal. For example, in a high – temperature furnace environment with a lot of oxygen present, a heat – resistant stainless steel wire rope with a sufficient chromium content can maintain its integrity for a long time. A typical heat – resistant stainless steel may contain 18 – 25% chromium. The higher the chromium content within a certain range, the better the oxidation resistance at high temperatures.
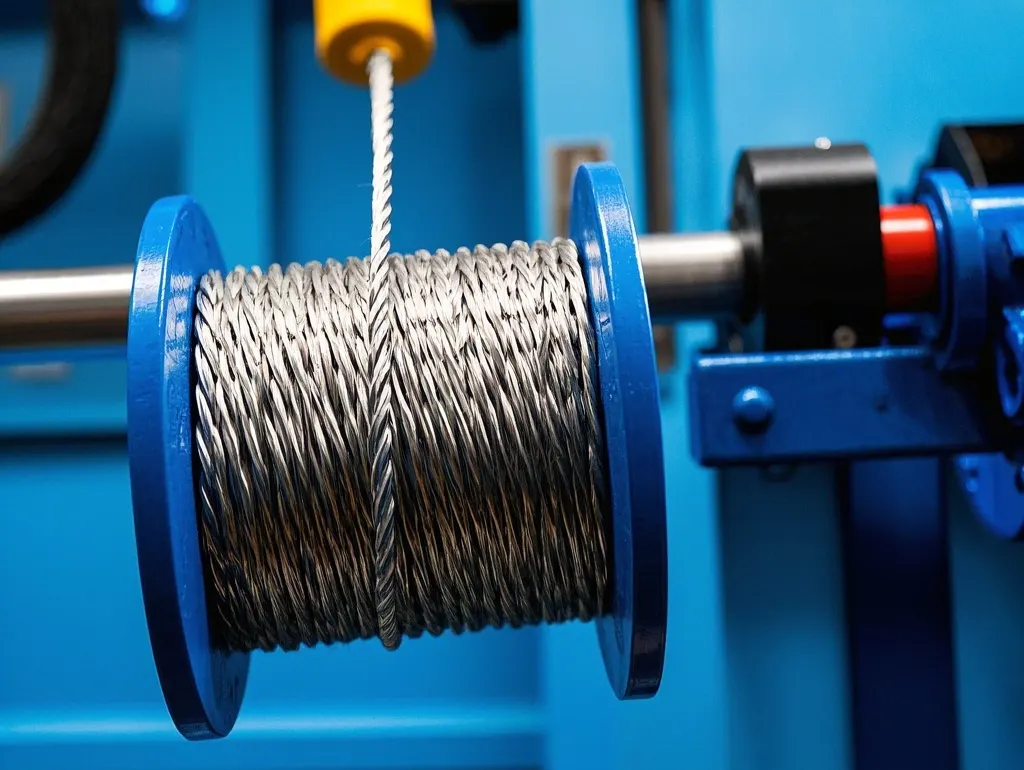
Nickel (Ni) is another important alloying element. Nickel improves the overall toughness and ductility of the stainless steel at high temperatures. It also enhances the stability of the austenitic structure in austenitic stainless steels, which are commonly used in heat – resistant applications. Austenitic stainless steels with a significant nickel content can better withstand thermal cycling and mechanical stresses at high temperatures. For instance, in aerospace applications where the wire ropes may experience rapid temperature changes during flight, the presence of nickel ensures that the wire ropes do not become brittle and break under such conditions. A common heat – resistant austenitic stainless steel might have 8 – 15% nickel.
Molybdenum (Mo) is added to increase the corrosion resistance, especially in aggressive environments at high temperatures. It improves the steel’s resistance to pitting and crevice corrosion. In power generation plants where the wire ropes may be exposed to hot, corrosive gases and steam, molybdenum – containing heat – resistant stainless steel wire ropes can provide better long – term performance. Usually, the molybdenum content in heat – resistant stainless steels ranges from 2 – 5%.
2. Structural Features
The structure of a heat – resistant stainless steel wire rope has a significant impact on its mechanical properties and high – temperature stability.
Most heat – resistant stainless steel wire ropes consist of multiple strands. A common configuration is a 6 – strand structure, where each strand is composed of a certain number of individual wires. For example, a strand may contain 19 or 37 wires. The number of wires in a strand affects the flexibility and load – bearing capacity of the wire rope. A larger number of wires in a strand generally results in a more flexible wire rope, which can be beneficial in applications where the wire rope needs to bend around pulleys or other components. However, it may also slightly reduce the overall strength compared to a strand with fewer but thicker wires.
The wires within each strand are typically helically wound around a central core wire or a fiber core. This helical winding provides the wire rope with its characteristic strength and flexibility. The pitch of the helix (the distance along the length of the strand for one complete turn of the wire) is carefully designed. A smaller pitch means the wires are more closely packed, resulting in a stronger and more compact strand but less flexible. In high – temperature applications, a proper pitch is crucial to ensure that the wire rope can maintain its structural integrity under thermal expansion and contraction.
The strands are then helically laid around a central core to form the complete wire rope. The way the strands are laid (right – hand lay or left – hand lay) can also influence the performance of the wire rope. A right – hand lay wire rope will tend to rotate in a certain direction when under load, and this needs to be considered in the design of the systems using the wire rope. Additionally, some wire ropes may have a special outer layer of wires or a coating to further enhance their wear resistance or corrosion resistance at high temperatures. This complex structure allows heat – resistant stainless steel wire ropes to combine high strength, flexibility, and the ability to withstand high – temperature environments, making them suitable for a wide range of industrial applications.
Key High-Temperature Performance Parameters
1. Tensile Strength at High Temperatures
Tensile strength at high temperatures refers to the maximum stress that a heat – resistant stainless steel wire rope can withstand under tension without breaking when exposed to elevated temperatures. This parameter is crucial as it determines the load – bearing capacity of the wire rope in high – temperature applications.
Experimental data shows that as the temperature increases, the tensile strength of heat – resistant stainless steel wire ropes generally decreases. For example, in a study on a specific type of heat – resistant stainless steel wire rope with a nominal tensile strength of 1500 MPa at room temperature, when the temperature reaches 500°C, the tensile strength may drop to around 1200 MPa. As the temperature further rises to 800°C, the tensile strength could be reduced to approximately 800 MPa.
The following graph (Figure 1) visually represents this trend:
Temperature (°C) | Tensile Strength (MPa) |
25 | 1500 |
300 | 1350 |
500 | 1200 |
700 | 1000 |
800 | 800 |
Figure 1: Tensile Strength Variation with Temperature
Several factors contribute to this decrease in tensile strength at high temperatures. The first is the softening of the metal lattice structure. As the temperature rises, the atoms in the stainless steel gain more thermal energy, which leads to increased atomic mobility. This increased mobility weakens the inter – atomic bonds, reducing the overall strength of the material. Additionally, the precipitation of certain phases within the steel, such as carbides, can also affect the tensile strength. At high temperatures, these carbides may grow in size or change their distribution, disrupting the uniform structure of the steel and causing a reduction in strength.
2. Creep Resistance
Creep is the time – dependent plastic deformation that occurs in a material when it is subjected to a constant load at an elevated temperature for an extended period. In the context of heat – resistant stainless steel wire ropes, creep can be a critical issue, especially in applications where the wire ropes are under continuous stress in high – temperature environments.
When a wire rope is under a constant tensile load at high temperatures, the metal atoms gradually start to move and rearrange themselves. This movement is facilitated by the high – temperature – induced thermal energy. For example, in a power plant where a heat – resistant stainless steel wire rope is used to support a heavy component in a steam – filled environment at around 600 – 700°C, over time, the wire rope may gradually stretch due to creep.
The evaluation of creep performance in heat – resistant stainless steel wire ropes typically involves parameters such as creep rate and creep rupture life. The creep rate is the rate at which the deformation occurs over time, usually expressed as a percentage increase in length per unit time. Creep rupture life, on the other hand, is the time it takes for the wire rope to break under the given high – temperature and constant – load conditions.
To measure these parameters, standardized creep tests are conducted. In a typical creep test, a specimen of the wire rope is subjected to a constant tensile load in a high – temperature furnace. The elongation of the specimen is measured at regular intervals over an extended period. By analyzing the data obtained from these measurements, the creep rate and creep rupture life can be determined. These test results are then used to assess the suitability of the wire rope for specific high – temperature applications. For instance, if a wire rope has a high creep rate and a short creep rupture life, it may not be suitable for long – term, high – load applications in high – temperature environments.
3. Thermal Expansion Coefficient
The thermal expansion coefficient is a measure of how much a material expands or contracts in response to a change in temperature. For heat – resistant stainless steel wire ropes, this parameter is of great importance as it affects the dimensional stability of the wire rope in high – temperature environments.
A high – thermal – expansion – coefficient material will expand significantly when heated and contract when cooled. In the case of a heat – resistant stainless steel wire rope, if the thermal expansion coefficient is too large, during the heating – up process in a high – temperature application, the wire rope may experience excessive expansion. This can lead to issues such as changes in the tension of the wire rope, misalignment in the pulley systems it is used with, or even mechanical failure if the expansion is not properly accounted for.
Different heat – resistant stainless steel materials have different thermal expansion coefficients. For example, austenitic heat – resistant stainless steels generally have a relatively higher thermal expansion coefficient compared to ferritic heat – resistant stainless steels. Austenitic stainless steels may have a thermal expansion coefficient in the range of 16 – 18 × 10⁻⁶/°C, while ferritic stainless steels might have a value in the range of 10 – 12 × 10⁻⁶/°C.
The following table (Table 1) shows the thermal expansion coefficients of some common heat – resistant stainless steel materials:
Stainless Steel Type | Thermal Expansion Coefficient (× 10⁻⁶/°C) |
Austenitic 310S | 17.5 |
Ferritic 446 | 11.5 |
Martensitic 420 | 10.5 – 11.5 |
Table 1: Thermal Expansion Coefficients of Common Heat – Resistant Stainless Steels
These differences in thermal expansion coefficients need to be carefully considered when selecting heat – resistant stainless steel wire ropes for specific applications. For applications where dimensional stability is crucial, such as in precision machinery in high – temperature environments, a material with a lower thermal expansion coefficient may be preferred to minimize the effects of thermal expansion and contraction.
4. Oxidation Resistance
At high temperatures, heat – resistant stainless steel wire ropes are prone to oxidation. The oxidation process occurs when the iron and other alloying elements in the stainless steel react with oxygen in the surrounding atmosphere. This reaction forms metal oxides on the surface of the wire rope. For example, iron in the stainless steel reacts with oxygen to form iron oxides such as Fe₂O₃ and Fe₃O₄.
The main indicator for measuring the oxidation resistance of heat – resistant stainless steel wire ropes is the oxidation rate, which is usually expressed as the mass gain per unit area of the wire rope surface over a certain period of time when exposed to high – temperature oxygen – containing environments. A lower oxidation rate indicates better oxidation resistance.
Alloying elements play a significant role in enhancing the oxidation resistance of heat – resistant stainless steel wire ropes. As mentioned earlier, chromium forms a dense and adherent chromium oxide layer on the surface. This layer acts as a barrier, preventing further oxygen from reaching the underlying metal and thus slowing down the oxidation process. Nickel also contributes to oxidation resistance by improving the stability of the passive oxide layer. Molybdenum can enhance the resistance to pitting corrosion during the oxidation process, especially in environments with aggressive media.
Surface treatments can also improve the oxidation resistance of wire ropes. For example, passivation treatments can be applied to the surface of the wire ropes. Passivation involves creating a thin, protective oxide layer on the surface through chemical treatment. This layer can further enhance the oxidation resistance of the wire rope. Additionally, coatings such as ceramic coatings can be applied to the wire rope surface. These coatings provide an extra physical barrier against oxygen, significantly improving the wire rope’s ability to withstand high – temperature oxidation. In high – temperature furnace applications, wire ropes with such surface treatments can have a much longer service life compared to those without them.
Factors Affecting High-Temperature Performance
1. Temperature
Temperature is a primary factor influencing the high – temperature performance of heat – resistant stainless steel wire ropes. As the temperature rises, the material undergoes several microstructural and mechanical property changes.
At relatively low – elevated temperatures (up to around 300 – 400°C), the main effect is the activation of dislocations within the metal lattice. Dislocations are defects in the crystal structure of the metal, and at higher temperatures, they can move more freely. This increased mobility can lead to a phenomenon called work – hardening, where the metal becomes stronger as the dislocations interact and accumulate. However, as the temperature continues to increase, above 400°C, the thermal energy becomes sufficient to start annealing the material. Annealing is a process that reverses the work – hardening effect. The dislocations start to rearrange and annihilate each other, causing the material to soften.
For example, in a study of a heat – resistant stainless steel wire rope used in a heat – treatment furnace operating at 600°C, after continuous exposure for several hundred hours, the wire rope’s microstructure showed signs of grain growth. Larger grains mean a reduction in the number of grain boundaries. Grain boundaries are important for strengthening the material as they act as barriers to dislocation movement. With fewer grain boundaries, the material becomes more prone to plastic deformation, leading to a decrease in tensile strength.
At extremely high temperatures, close to the melting point of the stainless steel alloy, the metal lattice can start to break down, and the material loses its integrity rapidly. The mechanical properties such as tensile strength and yield strength drop significantly, and the wire rope may no longer be able to perform its intended function.
2. Loading Conditions
The type of loading and the loading rate have a significant impact on the high – temperature performance of heat – resistant stainless steel wire ropes.
Static Loading: Under static loading conditions, where a constant load is applied to the wire rope at high temperatures, creep becomes a major concern. As mentioned earlier, creep is the time – dependent plastic deformation. In a power – plant application, if a heat – resistant stainless steel wire rope is used to support a heavy steam – pipe at a high temperature (say 550 – 650°C), over time, the wire rope will gradually elongate due to creep. The longer the wire rope is exposed to the high – temperature and static load, the more significant the creep deformation will be. Eventually, if the creep deformation exceeds the allowable limit, the wire rope may fail, leading to potential safety hazards and equipment damage.
Dynamic Loading: Dynamic loading involves the application of varying loads. In applications such as in the aerospace industry, where wire ropes are used in the landing gear systems of aircraft, during take – off and landing, the wire ropes are subjected to dynamic loads. At high temperatures, the repeated application and removal of these dynamic loads can lead to fatigue failure. Fatigue occurs when the material experiences cyclic stress – strain cycles. The high – temperature environment exacerbates the fatigue process. The thermal energy at high temperatures can cause the initiation and growth of cracks at a faster rate compared to room – temperature conditions. Micro – cracks can form at stress – concentration points such as the surface of the wire or at the interfaces between different strands. These cracks can then propagate under the influence of the dynamic loads, eventually leading to the fracture of the wire rope.
Cyclic Loading: Cyclic loading is a specific type of dynamic loading with a regular pattern of load application and removal. In a metallurgical furnace that uses a heat – resistant stainless steel wire rope for a lifting mechanism that operates in a cyclic manner (lifting and lowering hot metal objects at regular intervals), the cyclic loading at high temperatures can cause the wire rope to experience stress – relaxation. Stress – relaxation is the decrease in stress over time while the strain is held constant. In the context of a wire rope under cyclic loading at high temperatures, the internal stresses within the wire rope will gradually decrease. This can lead to a change in the tension of the wire rope, affecting the stability of the lifting operation. If the stress – relaxation is not properly accounted for, it can result in the wire rope becoming slack or even losing its load – bearing capacity over time.
The loading rate also plays a role. A high – loading rate can cause the material to respond differently compared to a low – loading rate. At high – loading rates, the material may not have enough time to undergo the necessary microstructural changes to accommodate the stress. This can lead to a more brittle behavior, even at high temperatures where the material would otherwise be more ductile under a lower – loading rate. For example, in a high – speed industrial process where a heat – resistant stainless steel wire rope is suddenly subjected to a large load at high temperature, the wire rope may fail due to the inability of the material to distribute the stress effectively, resulting in a rapid fracture.
3. Environment
The high – temperature environment in which the heat – resistant stainless steel wire ropes operate can have a profound impact on their performance.
Chemical Substances: In industrial settings, wire ropes may be exposed to various chemical substances at high temperatures. For instance, in chemical plants or refineries, the wire ropes can come into contact with corrosive gases such as sulfur dioxide (SO₂), hydrogen sulfide (H₂S), or acidic vapors. These chemical substances can react with the stainless steel, attacking the protective oxide layer on the surface. When the oxide layer is damaged, the underlying metal becomes vulnerable to further corrosion. Sulfur – containing gases can react with the chromium in the stainless steel to form chromium sulfides. These sulfides are not as protective as the chromium oxide layer and can lead to pitting corrosion. Pitting corrosion is a localized form of corrosion that creates small pits on the surface of the wire rope. These pits can act as stress – concentration points, reducing the overall strength of the wire rope and increasing the likelihood of failure.
Atmospheric Conditions: The atmosphere in high – temperature environments can be either oxidizing or reducing, and this has a significant impact on the performance of the wire ropes. In an oxidizing atmosphere, such as in a high – temperature furnace with a large amount of oxygen present, the oxidation of the stainless steel is enhanced. Although stainless steels are designed to form a protective oxide layer, in a highly oxidizing and high – temperature environment, the oxidation rate can still be significant. The continuous growth of the oxide layer can lead to a loss of material from the surface of the wire rope. This not only reduces the cross – sectional area of the wire rope, thereby decreasing its load – bearing capacity, but also can cause the wire rope to become brittle due to the formation of a thick, non – adherent oxide layer.
In a reducing atmosphere, such as in some metal – smelting processes where there is a lack of oxygen and an abundance of reducing agents like carbon monoxide (CO), the protective oxide layer on the stainless steel can be reduced. This exposes the underlying metal to potential corrosion and degradation. Additionally, in a reducing atmosphere, some alloying elements in the stainless steel may react with the reducing agents, leading to changes in the chemical composition and microstructure of the material, which in turn can affect its mechanical properties. For example, in a high – temperature environment with a reducing atmosphere, the nickel in the stainless steel may react with carbon monoxide to form nickel carbonyl compounds. This can lead to a loss of nickel from the alloy, changing its properties and reducing its corrosion resistance and high – temperature performance.
Testing and Evaluation Methods
1. Laboratory Testing
Laboratory testing is a fundamental approach to accurately assess the high – temperature performance parameters of heat – resistant stainless steel wire ropes.
High – Temperature Tensile Testing:
- Equipment: A universal testing machine equipped with a high – temperature furnace is used. The furnace can heat the wire rope specimen to the desired high – temperature range, typically up to 1000°C or more, depending on the requirements. The testing machine is capable of applying a tensile force to the specimen at a controlled rate.
- Testing Procedure: First, a wire rope specimen of a specific length and diameter is prepared. The specimen is then placed inside the high – temperature furnace of the testing machine. The furnace is heated to the target temperature and allowed to stabilize for a certain period to ensure uniform temperature distribution within the specimen. Once the temperature is stable, the tensile force is gradually applied to the specimen at a constant rate, such as 0.5 mm/min.
- Data Collection and Analysis: During the test, the load applied to the specimen and the corresponding elongation are continuously measured. The data is recorded in real – time. After the specimen fractures, the tensile strength at the high – temperature is calculated by dividing the maximum load reached during the test by the original cross – sectional area of the specimen. The stress – strain curve can also be plotted, which provides insights into the material’s behavior under tensile load at high temperatures, such as the yield strength, elongation at break, and the modulus of elasticity.
Creep Testing:
- Equipment: A creep testing machine with a high – temperature chamber is essential. This machine can maintain a constant tensile load on the wire rope specimen while the specimen is exposed to a high – temperature environment. The temperature in the chamber can be precisely controlled, and the elongation of the specimen is monitored over time.
- Testing Procedure: A wire rope specimen is installed in the creep testing machine. A specific tensile load is applied to the specimen, and the high – temperature chamber is heated to the test temperature. The test may last for hundreds or even thousands of hours, depending on the requirements.
- Data Processing: The elongation of the specimen is measured at regular intervals, such as every hour or every few hours. The creep rate is calculated by dividing the change in length of the specimen over a certain time interval by the original length of the specimen and the time interval. The creep rupture life is determined as the time when the specimen finally breaks under the constant load and high – temperature conditions. By analyzing the creep data, the creep behavior of the heat – resistant stainless steel wire rope can be understood, and predictions can be made about its long – term performance in high – temperature applications.
Thermal Expansion Testing:
- Equipment: A dilatometer is commonly used for measuring the thermal expansion of heat – resistant stainless steel wire ropes. A dilatometer can accurately measure the change in length of a specimen as the temperature changes.
- Testing Procedure: A small wire rope specimen is placed in the dilatometer. The temperature of the specimen is gradually increased from room temperature to the desired high – temperature range at a controlled rate, for example, 5°C/min.
- Data Analysis: The change in length of the specimen is continuously monitored and recorded as a function of temperature. The thermal expansion coefficient is calculated by dividing the change in length of the specimen by the original length and the change in temperature. This value helps in understanding how the wire rope will expand or contract in high – temperature environments and is crucial for designing systems where dimensional stability is important.
Oxidation Resistance Testing:
- Equipment: A high – temperature furnace with a controlled atmosphere is used. The furnace can be filled with an oxidizing gas, such as air or oxygen, to simulate the high – temperature oxidation environment. A precision balance is also required to measure the mass of the wire rope specimen before and after the oxidation test.
- Testing Procedure: A wire rope specimen is weighed accurately and then placed in the high – temperature furnace. The furnace is heated to the test temperature, and the specimen is exposed to the oxidizing atmosphere for a specific period, which could range from several hours to days.
- Data Evaluation: After the test, the specimen is removed from the furnace and cooled to room temperature. It is then weighed again. The oxidation rate is determined by calculating the mass gain per unit area of the specimen surface over the test period. A lower oxidation rate indicates better oxidation resistance of the heat – resistant stainless steel wire rope.
2. Field Testing
Field testing involves evaluating the performance of heat – resistant stainless steel wire ropes in real – world high – temperature industrial environments.
Testing Methods:
- In a power generation plant, for example, a heat – resistant stainless steel wire rope used in a steam turbine or boiler is monitored during normal operation. Parameters such as the tension of the wire rope, its elongation over time, and any signs of surface damage or corrosion are observed. Specialized sensors can be installed to measure the tension of the wire rope continuously. Infrared thermography can be used to monitor the temperature distribution along the wire rope to ensure that it is within the acceptable range.
- In a metallurgical furnace, the wire ropes used for lifting and transporting hot metal products are inspected regularly. The number of lifting cycles, the maximum load lifted, and the temperature of the wire rope during operation are recorded. Visual inspections are carried out to check for any signs of wear, cracking, or oxidation on the surface of the wire rope.
Precautions:
- Safety is of utmost importance during field testing. Workers involved in the testing must wear appropriate personal protective equipment, such as heat – resistant clothing, gloves, and safety goggles, to protect themselves from the high – temperature environment and potential hazards associated with the wire ropes.
- The testing equipment used in the field must be reliable and suitable for the harsh industrial conditions. Calibration of the sensors and measuring devices should be carried out regularly to ensure accurate data collection.
- Environmental factors in the field, such as dust, humidity, and the presence of other chemical substances, need to be considered. These factors can affect the performance of the wire ropes and the accuracy of the test results. For example, high humidity in a power – plant environment can accelerate the corrosion process of the wire ropes, especially if there are any flaws in the protective oxide layer.
Field testing is crucial as it provides real – time data on how the heat – resistant stainless steel wire ropes perform in actual operating conditions. This data complements the laboratory – test results and helps in validating the design and selection of wire ropes for specific high – temperature applications. It also allows for the identification of any unforeseen issues that may not have been apparent in the laboratory, such as the interaction between the wire ropes and the surrounding industrial equipment or the long – term effects of the complex industrial environment on the wire rope’s performance.
Applications and Significance
1. Industrial Applications
Heat – resistant stainless steel wire ropes find extensive applications in various industries due to their unique high – temperature performance.
Energy Industry: In power generation plants, especially in coal – fired power plants and nuclear power plants, heat – resistant stainless steel wire ropes play a crucial role. In coal – fired power plants, they are used in the coal – handling systems. For example, the wire ropes are employed in conveyor belts that transport coal from the storage area to the boilers. These wire ropes need to withstand high – temperature environments generated during the combustion process, which can reach up to 800 – 1000°C in some areas near the boilers. Their high – temperature tensile strength ensures that they can carry the heavy loads of coal continuously without breaking. In nuclear power plants, heat – resistant stainless steel wire ropes are used in the control rod drive mechanisms. These mechanisms are responsible for inserting and withdrawing the control rods that regulate the nuclear reaction. The wire ropes must maintain their mechanical properties in the high – temperature and radiation – intensive environment inside the nuclear reactor. The creep resistance of the wire ropes is of utmost importance here, as any deformation over time could lead to malfunctions in the control rod movement, potentially endangering the safety of the entire nuclear power plant.
Aerospace Industry: In aerospace applications, heat – resistant stainless steel wire ropes are essential components. During the re – entry of spacecraft into the Earth’s atmosphere, the wire ropes used in the parachute deployment systems are exposed to extremely high temperatures. The intense heat generated by air friction can cause the temperature around the wire ropes to exceed 1500°C. The oxidation resistance of the heat – resistant stainless steel wire ropes is critical in this scenario. The protective oxide layer formed on the surface of the wire ropes due to the alloying elements like chromium helps prevent rapid oxidation and degradation of the wire ropes. If the wire ropes were to lose their integrity during parachute deployment, it could result in a catastrophic failure of the spacecraft’s landing system. Additionally, in aircraft engines, wire ropes are used in the engine control systems. They need to operate in high – temperature environments within the engine, where the temperature can reach 1000 – 1200°C. The high – temperature tensile strength and fatigue resistance of the wire ropes ensure the smooth operation of the engine control mechanisms, allowing for precise control of the engine’s thrust and other parameters.
Metallurgical Industry: In the metallurgical industry, high – temperature furnaces are commonly used for metal smelting and heat – treatment processes. Heat – resistant stainless steel wire ropes are used for lifting and transporting hot metal products. For instance, in a steel – making furnace, the wire ropes are used to lift molten steel ladles. The ladles can weigh several tons, and the wire ropes need to have high – temperature tensile strength to support such heavy loads. The temperature of the molten steel can be around 1500°C, and the wire ropes must maintain their strength and stability in this extremely high – temperature environment. Moreover, in continuous casting processes, wire ropes are used in the machinery that pulls the semi – solid metal through the casting molds. The thermal expansion coefficient of the wire ropes is an important factor here. If the wire ropes expand too much due to the high – temperature of the metal, it can lead to misalignment and defects in the casting process.
2. Significance of Understanding Performance Parameters
Understanding the high – temperature performance parameters of heat – resistant stainless steel wire ropes is of great significance in several aspects.
Product Design: In product design, accurate knowledge of the performance parameters allows engineers to design systems that are safe and reliable. For example, when designing a lifting mechanism in a high – temperature industrial furnace, the engineer needs to know the high – temperature tensile strength of the wire ropes to determine the appropriate diameter and number of wire ropes required to lift the intended load. If the tensile strength is underestimated, the wire ropes may break during operation, causing damage to the equipment and potential safety hazards. On the other hand, if the tensile strength is overestimated, it may lead to over – engineering, increasing the cost and complexity of the system. The creep resistance parameter is also crucial in product design. In applications where the wire ropes are under continuous load at high temperatures for long periods, such as in a power – plant steam – pipe support system, the creep rate and creep rupture life need to be considered. By knowing these parameters, engineers can design the support system in a way that ensures the wire ropes can maintain their position and support the steam pipes without excessive deformation over the expected service life of the system.
Material Selection: Performance parameters are essential for selecting the right heat – resistant stainless steel wire rope for a specific application. Different applications have different requirements in terms of temperature, load, and environment. For example, in a chemical plant where the wire ropes are exposed to both high – temperature and corrosive chemicals, a wire rope with high oxidation resistance and corrosion resistance is required. By comparing the oxidation resistance and corrosion – resistance performance parameters of different heat – resistant stainless steel wire ropes, the most suitable material can be chosen. In an aerospace application where weight is a critical factor, a wire rope with high strength – to – weight ratio and good high – temperature performance needs to be selected. Understanding the thermal expansion coefficient helps in choosing a wire rope that will not cause dimensional stability issues in the application. For example, in a precision instrument in a high – temperature environment, a wire rope with a low thermal expansion coefficient is preferred to ensure accurate operation.
Safety Assurance: Safety is a top priority in all industrial applications. Understanding the high – temperature performance parameters of heat – resistant stainless steel wire ropes is crucial for ensuring safety. In applications such as in nuclear power plants or aerospace, the failure of a wire rope can have catastrophic consequences. By knowing the fatigue resistance, creep resistance, and high – temperature tensile strength of the wire ropes, proper safety factors can be incorporated into the design. Regular testing and monitoring of these performance parameters during the operation of the wire ropes can also help detect any potential issues early. For example, if the oxidation rate of a wire rope in a high – temperature furnace exceeds the acceptable limit, it may indicate that the wire rope is at risk of failure, and appropriate measures can be taken, such as replacing the wire rope or improving the protective coating, to prevent a safety incident.
Conclusion
In summary, heat – resistant stainless steel wire ropes are indispensable components in numerous high – temperature industrial applications. Their performance in such environments is determined by a combination of factors, including material composition, structural features, and key high – temperature performance parameters.
The material composition, with elements like chromium, nickel, and molybdenum, endows the wire ropes with high – temperature and corrosion – resistant properties. The structural design, from the number of wires in a strand to the way the strands are laid around the core, affects their mechanical and high – temperature stability. The key high – temperature performance parameters, such as tensile strength at high temperatures, creep resistance, thermal expansion coefficient, and oxidation resistance, play a crucial role in determining the wire ropes’ suitability for specific applications. Temperature, loading conditions, and the environment all have a significant impact on these performance parameters, and understanding these effects is essential for optimizing the use of heat – resistant stainless steel wire ropes.
Laboratory testing methods, including high – temperature tensile testing, creep testing, thermal expansion testing, and oxidation resistance testing, provide accurate data on the performance parameters. Field testing in real – world industrial environments complements these laboratory results, offering insights into the wire ropes’ long – term performance and any unforeseen issues in actual operation.
The applications of heat – resistant stainless steel wire ropes span multiple industries, such as the energy, aerospace, and metallurgical industries. Understanding their high – temperature performance parameters is of great significance for product design, material selection, and safety assurance. In product design, it ensures the creation of safe and reliable systems; in material selection, it helps choose the most suitable wire ropes for different applications; and in safety assurance, it plays a vital role in preventing catastrophic failures.
Future research in this area could focus on several directions. First, developing new heat – resistant stainless steel alloys with even better high – temperature performance is a promising area. This could involve exploring new alloying elements or optimizing the existing alloy compositions to further enhance properties like tensile strength, creep resistance, and oxidation resistance at higher temperatures. Second, improving the manufacturing processes of wire ropes to achieve more uniform microstructures and better – controlled structural features. This could lead to more consistent high – temperature performance and longer service lives. Third, conducting more in – depth research on the interaction between heat – resistant stainless steel wire ropes and complex high – temperature environments, especially in the presence of multiple chemical substances and extreme atmospheric conditions. This would help in developing more effective protective coatings and surface treatments to improve the wire ropes’ performance and durability in such harsh environments. Overall, continuous research and development in this field will be crucial for meeting the growing demands of high – temperature applications in various industries.
Leave a Reply