Rectangular tubing, a hollow long steel material, is also known as flat tube, flat square tube, or square flat tube. It offers the advantage of being lighter while maintaining comparable bending and torsional strength, making it widely used in manufacturing mechanical parts, engineering structures, and various other applications. In the United States and globally, ASTM (American Society for Testing and Materials) standards play a crucial role in ensuring the quality, consistency, and safety of rectangular tubing. These standards cover a wide range of aspects, including material composition, mechanical properties, dimensions, and manufacturing processes.
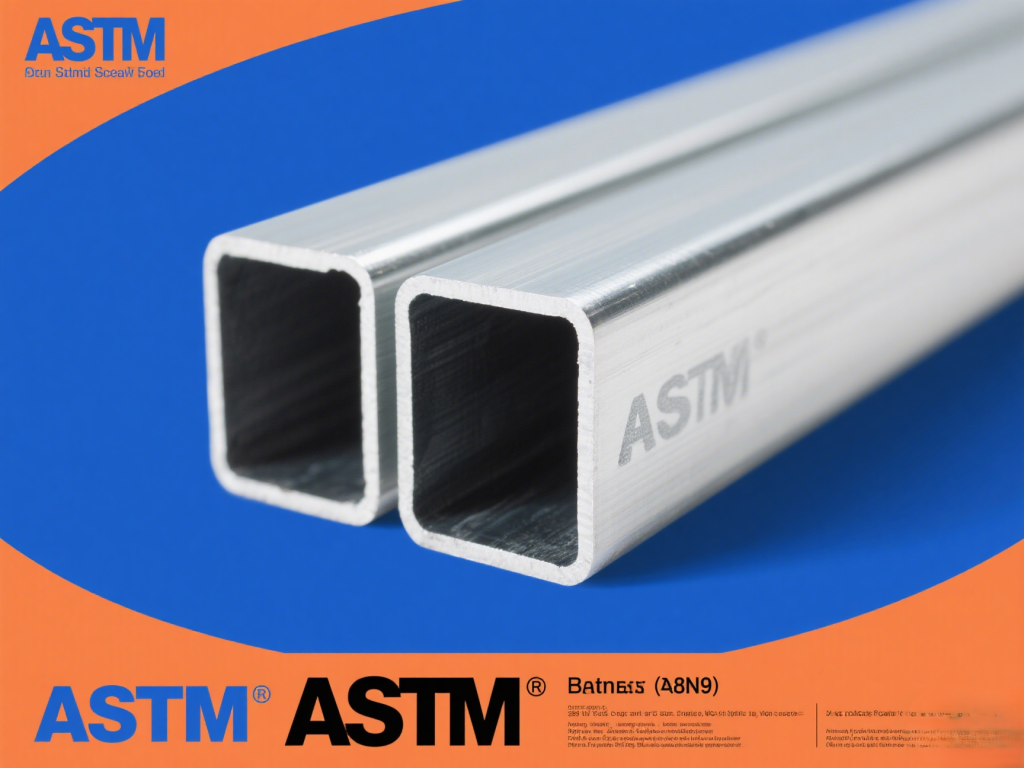
2. Key ASTM Standards for Rectangular Tubing
2.1 ASTM A500
- General Overview: ASTM A500 is a standard specification for seamless and weldable carbon structural steel published by ASTM International. It covers cold – formed welded and seamless carbon steel round, square, rectangular, or special – shape structural tubing. This tubing is intended for use in welded, riveted, or bolted construction of bridges, buildings, and for general structural purposes.
- Tensile Properties:
- Minimum Tensile Strength: For ASTM A500 rectangular tubes, the minimum tensile strength values can vary. For example, in some cases, it can be 310 MPa, 400 MPa, 427 MPa, or 400 MPa depending on specific grades and conditions.
- Yield Strength: The yield strength also has different values such as 269 MPa, 317 MPa, 345 MPa, or 250 MPa. These values are critical as they determine the stress at which the material begins to deform plastically.
- Elongation: The minimum elongation per 50.8 mm (% d) also varies. For steel pipes with wall thickness (t) ≥ 3.05 mm, the minimum elongation is 25% (condition a). For thinner steel pipes in this condition, the minimum elongation can be calculated by the formula: secondary length per 50.8 mm = 56t + 17.5, rounded to two decimal places. For pipes with wall thickness (t) ≥ 4.57 mm, the minimum elongation is 13% (condition b), and for thinner pipes, the formula is elongation per 50.8 mm = 61t + 12, rounded to two decimal places. For pipes with wall thickness (t) ≥ 3.05 mm under condition c, the minimum elongation can be agreed with the manufacturer for thinner tubes. It should be noted that the specified minimum elongation is mainly a reference value for test experiments and not a technical standard for steel pipe trade.
- Applications: Due to its structural integrity and versatility, ASTM A500 rectangular tubing is commonly used in building frameworks, bridge components, and general construction where structural support is required.
2.2 ASTM A513
- Material and Use: ASTM A513 covers electric resistance welded carbon and alloy steel tubing for use as mechanical tubing. This standard is applicable to mechanical tubing made from hot or cold – rolled steel and includes round, square, rectangular, and special – shape tubing. Rectangular tubing under this standard is often used in applications where mechanical strength and precision are required.
- Material Properties: The material is typically carbon or alloy steel, which provides good compressive and tensile properties. In terms of specifications, the rectangular tubing can have various dimensions to suit different mechanical applications. For example, in building structures, it can be used for the support of beams and columns and the construction of frames, offering good load – bearing capacity. In machinery manufacturing, it is used to make machine tool structures, conveying equipment, and storage racks, owing to its good wear – resistance and corrosion – resistance properties.
2.3 ASTM B372 (for Copper and Copper – Alloy Rectangular Tubing)
- Specific Application: ASTM B372 – 22 is a standard specification for seamless copper and copper – alloy rectangular wave – guide tube. This type of rectangular tubing is used as a transmission line in electronic equipment.
- Material Composition: It specifies five materials with different nominal compositions. For instance, C10100 (copper, OFEA) has a nominal copper content of 99.99%, C10200 (copper, OFA) has 99.95% copper, and C10300 (copper, OFXLPA) has 99.95% copper along with 0.003% of other elements. These different compositions are tailored to meet the specific electrical and physical requirements of electronic applications.
3. Dimensions and Tolerances
3.1 Size Ranges
Rectangular tubing comes in a wide variety of sizes. For example, in inches, common sizes can range from small dimensions like 1” x 1/2” to large ones such as 10” x 8”. In millimeters, sizes can range from 10 mm × 15 mm to 1000 mm × 800 mm. The wall thickness also varies, with some thin – walled tubing having thicknesses as low as 0.6 mm and thick – walled tubing reaching up to 30 mm or more, depending on the application and the relevant ASTM standard.
3.2 Tolerance Standards
ASTM standards define tight tolerances for the dimensions of rectangular tubing. The tolerances ensure that the tubing produced by different manufacturers can be used interchangeably in various applications. For example, the dimensional tolerances for the width, height, and wall thickness of rectangular tubing are specified to ensure that the tubing fits correctly in fabricated structures. Deviations from these tolerances can affect the performance of the tubing in applications such as structural support, where precise fits are necessary for proper load – distribution.
4. Manufacturing Process Requirements
4.1 Welded Tubing
- Welding Methods: For welded rectangular tubing, ASTM standards may specify acceptable welding methods such as electric resistance welding (ERW). In ERW, an electric current is passed through the edges of the steel strip as it is formed into a rectangular shape, heating and fusing the edges together. This process must be carefully controlled to ensure the integrity of the weld joint.
- Weld Quality: The quality of the weld is closely monitored. ASTM standards may require visual inspection for surface defects, as well as non – destructive testing methods such as ultrasonic testing or radiographic testing to detect internal weld flaws. The strength of the weld joint should also meet or exceed the minimum requirements specified in the standard to ensure the overall strength of the rectangular tubing.
4.2 Seamless Tubing
- Manufacturing Process: Seamless rectangular tubing is typically manufactured by hot – rolling or cold – drawing processes. In hot – rolling, a billet of steel is heated and passed through a series of rolling mills to form the desired rectangular shape. Cold – drawing involves pulling a pre – formed tube through a die to reduce its size and improve its surface finish and mechanical properties.
- Quality Control: During the manufacturing of seamless tubing, quality control measures are in place to ensure that the tubing meets the ASTM standards. This includes monitoring the temperature, rolling forces, and drawing speeds to control the microstructure and mechanical properties of the tubing. The surface of the seamless tubing should be free from defects such as cracks, pits, and scratches.
5. Testing and Inspection
5.1 Mechanical Testing
- Tensile Testing: Tensile testing is a fundamental test required by ASTM standards. A sample of the rectangular tubing is subjected to a gradually increasing tensile force until it fractures. The results of this test, including the yield strength, tensile strength, and elongation, are compared to the values specified in the relevant ASTM standard. For example, as per ASTM A500, the tensile properties of rectangular tubing must fall within the defined ranges.
- Bend Testing: Bend testing is used to evaluate the ductility and formability of the rectangular tubing. A sample is bent around a specified mandrel to a certain angle. The tubing should be able to withstand this bending without cracking or showing signs of excessive deformation, as per the requirements of the ASTM standard.
5.2 Chemical Analysis
- Composition Verification: Chemical analysis is performed to ensure that the material composition of the rectangular tubing meets the requirements of the ASTM standard. This is particularly important for alloys where the precise ratio of elements can significantly affect the mechanical and physical properties. For example, in copper – alloy rectangular tubing under ASTM B372, the chemical composition of the alloy must be within the specified limits to ensure proper performance in electronic applications.
5.3 Non – Destructive Testing
- Ultrasonic Testing: Ultrasonic testing is used to detect internal defects in the rectangular tubing, such as voids, inclusions, or cracks. High – frequency sound waves are transmitted through the tubing, and any reflections from defects are analyzed. This method is sensitive and can detect small defects that may not be visible on the surface.
- Magnetic Particle Testing: For ferromagnetic materials, magnetic particle testing can be used to detect surface and near – surface defects. A magnetic field is applied to the tubing, and magnetic particles are spread on the surface. The particles will accumulate at the sites of defects, making them visible. This technique is useful for detecting cracks and other discontinuities in the surface layer of the rectangular tubing.
6. Applications of Rectangular Tubing Meeting ASTM Standards
6.1 Construction Industry
- Building Structures: Rectangular tubing meeting ASTM standards is extensively used in building structures. In multi – story buildings, ASTM A500 or ASTM A513 rectangular tubing can be used for columns and beams. The high strength – to – weight ratio of these tubes allows for the construction of lightweight yet sturdy structures. For example, in modern office buildings, rectangular tubing frames can support the floors and roofs, providing stability and safety.
- Residential Construction: In residential construction, rectangular tubing is used for various purposes. It can be used to build the framework of garages, decks, and even some interior partitions. The use of ASTM – compliant tubing ensures that these structures are durable and can withstand the loads and environmental conditions they will be subjected to.
6.2 Mechanical and Manufacturing Industry
- Machine Frames: In the manufacturing of machinery, rectangular tubing is used to construct machine frames. ASTM A513 tubing, with its good mechanical properties, is ideal for this purpose. Machine frames need to be rigid and stable to ensure the proper functioning of the machinery. Rectangular tubing provides the necessary strength and can be easily fabricated into the required shapes.
- Conveyor Systems: Conveyor systems in factories and warehouses often use rectangular tubing. The tubing is used to build the support structures for the conveyor belts. The durability and strength of ASTM – standard rectangular tubing ensure that the conveyor systems can operate smoothly and efficiently, even when carrying heavy loads.
6.3 Automotive and Aerospace Industries
- Automotive Frames: Some automotive frames may use rectangular tubing, especially in high – performance or specialty vehicles. ASTM – compliant tubing can provide the necessary strength to withstand the stresses of vehicle operation while keeping the weight down, which is important for fuel efficiency and performance.
- Aerospace Components: In the aerospace industry, although less common than in other industries, rectangular tubing may be used in certain non – critical components or in the construction of ground support equipment. The strict quality control associated with ASTM standards ensures that the tubing used in these applications meets the high – reliability requirements of the aerospace sector.
7. Future Developments in ASTM Standards for Rectangular Tubing
ASTM International’s committee on steel, stainless steel, and related alloys (A01) is currently developing a proposed standard. This standard will provide requirements for precision sharp – cornered laser and laser – hybrid carbon steel square and rectangular tubes. It will also offer guidance on the specification of open sections used in architectural and industrial applications. The development of this standard is driven by the increasing use of such products in structural applications where extruded aluminum does not satisfy structural requirements, and where hot – rolled profiles or cold – formed rounded – corner carbon steel hollow structural sections do not provide the necessary precision. The use of these products can eliminate or reduce machining that might otherwise be required. Additionally, laser – fused profiles allow for a higher level of flexibility in terms of customization and do not have the minimum quantity requirements of conventional production methods. The proposed standard will be useful for both fabricators and designers who want to use precision sharp – cornered laser and laser – hybrid products. As technology continues to advance, ASTM standards for rectangular tubing are likely to evolve further to incorporate new manufacturing techniques, materials, and performance requirements, ensuring that rectangular tubing remains a reliable and versatile construction and manufacturing material.